About Us
Learn more about Hobas historyand management policies
History
From unlikely beginnings in the textile industry to
international supplier for infrastructure.
From an unlikely source, creative thinkers revolutionized two totally different industries. In the 1950s, the textile industry was still using wooden rollers in the dyeing process. Synthetic dyes, which had become popular in the late 1800s, accelerated warping and splintering of the wood cylinders used in the mass manufacture of dyed fabrics, damaging the fabric thus requiring frequent replacement. Engineers at the Basel Dye Works in Switzerland devised a method to centrifugally cast fiberglass reinforced plastic (FRP) cylinders. Thanks to this new method and material, they achieved perfectly concentric cylinders with a precise outer diameter and smooth, non-corrosive surfaces – just what the textile industry needed. While the textile industry was most impressed by the smooth exterior of the cylinder, it was the smooth interior that caught the attention of water conveyance engineers. Additionally, this high-strength pipe with its thin walls and light weight would make manufacture and installation much faster and less expensive. The process was patented and in 1960, Hobas Pipe was born.
It was not long before a team of Swiss engineers realized that the characteristics of these centrifugally cast GRP pipes would be the perfect material for a three-kilometer-long pressure pipeline (penstock) for a hydropower plant they were designing for Gommerkraftwerke AG to replace its deteriorated steel pipe. Located on a very steep Swiss mountainside in the Binn Valley in the Swiss canton of Valais, the DN 1000 mm (40-in) sloping pipeline was installed via open cut in 1961. The line remains in use to this day. Since that first penstock, many more have been constructed around the globe, including installations in the USA and Canada. Hobas centrifugally cast GRP pipe is manufactured and shipped to North America from the facility in Houston, Texas, which began production in 1987.
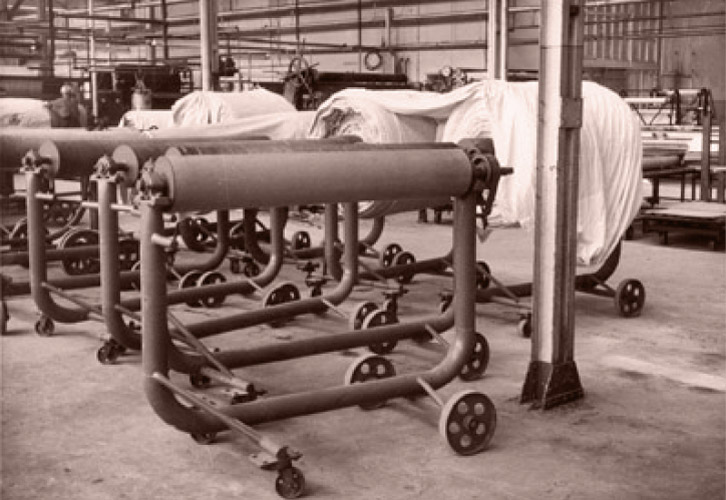
While the textile industry was most impressed by the smooth exterior of the cylinder, it was the smooth interior that caught the attention of water conveyance engineers. Additionally, this high-strength pipe with its thin walls and light weight would make manufacture and installation much faster and less expensive. The process was patented and in 1960, Hobas Pipe was born.
Quality Management
Energy & Environment
More about Hobas Pipe Commitment to Sustainability and Environmental Impact.
Amiblu pipes have a low carbon footprint compared to other pipe materials. (Hobas Pipe is a licensee of Amiblu.) This has been confirmed by external bodies and universities.
Comparison to other materials
An independent study conducted at the Norwegian University of Life Sciences in 2012 concludes that GRP pipes have a minimal negative environmental impact compared to other pipe materials. The main reason for this is the material efficiency.
Energy-efficient in operation
The smooth bore and good flow characteristics of Amiblu pipes reduce the amount of energy used for pumping. In penstocks, it increases the energy output.
Low energy consumption in production
The amount of energy used in the production of Amiblu pipes is less than what is required for most other pipe materials.
Efficient transportation
Lightweight design combined with the fact that Amiblu pipes can be nested during transportation lead to lower carbon emissions from pipe transportation.
Recyclable Amiblu pipes are recyclable.
The Federation of Reinforced Plastics in Germany recommends that GRP pipes are used e.g. in cement production.
Source: Amiblu Product Guide: Amiblu-Product-Guide.pdf